新视角|新形势下工厂设备管理的5大误区与对策
<
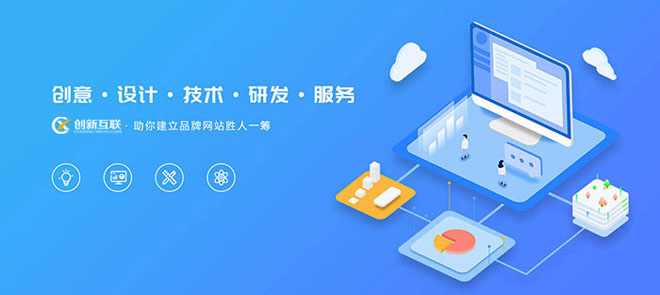
成都创新互联长期为上千多家客户提供的网站建设服务,团队从业经验10年,关注不同地域、不同群体,并针对不同对象提供差异化的产品和服务;打造开放共赢平台,与合作伙伴共同营造健康的互联网生态环境。为华安企业提供专业的网站设计、
成都做网站,
华安网站改版等技术服务。拥有10年丰富建站经验和众多成功案例,为您定制开发。div>在全球智能制造的浪潮下,我国制造业积极升级转型,自动化、数字化、网络化水平大大提高,生产设备日益走向集成化、智能化,设备数据可视化程度显著提高、操作上更加简单。但伴随而来的是设备的维护修理难度加大、维护成本提高,设备维护保养的作用也越来越凸显。在许多企业我们看到,企业花费巨资上马了非常先进的设备,而设备的管理维护、人员知识结构,仍停留在传统层面:数采基本靠笔,处理基本靠人,分析基本靠猜(经验)。可以说是买来了4.0的设备,延续着1.0的管理。
从设备资产效益产出角度看,我国制造业的设备综合效率的提升空间巨大。据统计,我国大部分离散制造业的OEE在60%左右,距离发达国家至少还有10%-20%的提升空间。同时,很多工厂对设备维护和保养的精细化管理不够重视CONTROL ENGINEERING China版权所有,这当中造成的异常停机和备件浪费等隐性损失,更是巨大的浪费。在当前疫情冲击、全球化局势不确定性进一步增加的形势下,这些效益改善空间www.cechina.cn,都可以为企业的生存、增强竞争力提供宝贵的机会。
图:离散制造业OEE现状评估
如何构建面向新型设备的管理能力,是当前制造业面临的一个问题和挑战。在这个过程中,我们总结了大家常常存在的5个误区,并给出了对应的策略建议,希望可以帮助企业少走一些弯路。
01 重硬轻软。
大部分企业新建工厂或者新购买的设备,只重视硬件的验收交接,忽视了软件的维护保养、校准标准,没有明确要求设备数据采集接口和设备数据所有权的诉求。根据工信部相关数据最新统计,目前我国企业生产设备的数字化率平均为47%,关键工艺的数控化率51%,关键设备联网率41%。嵌入式软件、人机界面、数据监测模型、管理平台都是新型设备的重要组成部分,都应是新型设备管理的范畴。从笔者进行工业互联网相关项目的经验看,设备的数据采集受制于工业现场协议众多、原厂不开放不支持、设备数据不确权等原因,设备数采仍然是生产现场数字化推进中成本最高的组成部分之一。比如我国许多SMT产线,贴片机本身精度很高、节拍很快、良率也都在99%以上了,单纯再靠手工调试,很难再提升了。许多工厂期望能将贴片机的数据实时数采和分析,解决自动叫料接料问题,改善抛料问题。但目前动辄数万的数采license费用,让许多工厂望而却步。
因此,工厂在设备采购环节就提前考虑,将相关要求加入商务条款,可以为以后设备制程详细数据的采集和分析优化做好准备。
02 生产为重,不坏不修、不停不管。
在大部分工厂,特别是离散制造业,都是生产是老大,设备只是保障部门,只要还能运转,就不会停产,这导致设备维护改善的时间和资金投入严重不足,设备部也陷入了四处救火、穷于应付的被动恶性循环。究其原因,是因为没有从工厂端到端视角看设备停机的损失。在设备初期征兆的时候介入维护,远比造成停机后再维护,造成的损失和投入成本要小的多。如下图,某机床通过振动分析,可以看到10月18日振动加速度峰值触发早期预警阈值,但是由于生产计划问题,没有停机维护;10月22日机床主控系统触发故障,不得不停机过10个小时维修和更换轴承,维修后,振动恢复正常水平,但巨大损失已经造成。
图:通过振动分析可以监测大部分机械故障
从设备管理大体经过的4个主要阶段来看,从1.0的纠正性维护(CM),到2.0预防性维护(PM)、3.0的可靠性维护(RCM)、4.0的预测性维护(PHM),本质上都是以设备健康管理(EHM)为中心,从“治已病”到“治未病”的进化过程。通过EHM,设备健康状态不再是被简单的划分为正常、异常。我们可以通过新技术、新工具控制工程网版权所有,分析积累的基础数据,评估出设备的亚健康状态,此时提前介入可以大大减少设备维护成本。例如,东智EHM给设备维护工程师配备带有振动传感器的智能点检仪,就像给医生配了“智能听诊器”一样,通过数秒的监测振动频谱,结合内置的频谱分析模型,就可以准确、快速的判断出设备健康状态、故障征兆原因,对故障辅助诊断起到重大作用。这样设备人的职责从原来的坏了维修www.cechina.cn,更多的转向如何保障设备健康运行的专业维保维护工作,进入良性循环。
03 设备问题就是设备部的事情。
虽然TPM已经推行了多年,但许多管理者观念和行动上,还是认为设备出了问题,就是设备部的事情,导致生产部门对设备的故障不关心,对影响产量、质量的设备维护不重视。设备维护工程师也往往低地位、低薪酬,自嘲为看门狗和替罪羊:节假日,别人可以休息,他们却不能离开,因为这正是维修设备的好时机;凡是出了问题,无论是设备停机,生产停产,还是质量事故,都会与设备相关,设备人员几乎永远是背锅的。为此,整个设备部成了优秀的人最不愿意去的地方。这种恶性循环现象,需要生产管理者身体力行树立正确的设备管理理念,构建生产为主体的全员自主维保体系。只有生产部门管理者重视起来了,全体生产设备操作者才能改变对设备漠不关心的态度,才能有效进行设备保养。而这个光靠设备部是玩不转的。
工厂可以通过引入设备健康管理EHM解决方案,构建全员自主维护保养体系,实现操作工的日常自主点检和保养、设备部的专业点检、设备故障扫码报修、扫码维护、维保工单自主抢单、维修效果用户评价、绩效竞比等功能和机制,帮助工厂实现TPM的自运转。
04 将设备维护当做成本中心,忽视了冰山下的损失。
许多管理者认为设备零故障是不可实现的,企业在遇到困难需要削减成本时,很多情况是拿设备维修费用开刀,甚至提出让维修预算每年递减百分之几的目标。从传统财务角度看,维修所消耗的资金一般被定义为成本和费用。其实早在30年前,德国召开欧洲维修团体联盟国际会议时,就提出“维修——为了未来的投资“的主题。作为投资,就需要有清晰的投入产出。维修的投入是设备日常维护所投入的人工费、各类防护费、备件费、设备管理相关系统。产出是什么呢?是由于设备维护不足、设备管理不善,带来的设备停机、精度或者质量缺陷带来的损失。如果对这些损失的价值误判,则容易扼杀设备维护技术和管理体系的改善性投入。
笔者曾经服务过一家大型工厂,设备部要上马EHM项目,实现设备的数据采集和监控,同时通过移动化的巡点检,实现设备的报修和维护过程,形成设备的故障树记录。在核算投入产出的时候,屡屡被财务挑战,过不了关。他们理解降低设备停机1小时的价值,仅仅是这1小时涉及到的员工的人工成本。这样算下来,价值产出太低,许多设备改善项目没法上马。而且这样的项目价值核算标准,直接打压了工厂精益革新的积极性。设备停机一小时的损失,要从工厂视角端到端的去衡量整体,这里面其实包括了产能损失的机会成本,即1小时的产品产值损失,才是这个工厂真正的损失。这样算下来,工厂许多可以改善停机、改善浪费、现场精益类的小改小革的项目,都可以得到了合理的开展,能激发起基层员工的创新积极性,也确实能给工厂带来实实在在的效益。
在实际操作中还存在一个问题,就是备件的更换很大程度上掌握在维修工手上,存在着许多“人为掌握”更换的因素。维修人员大都靠经验判别备件损坏程度,对怀疑有故障的零部件,通常为了减少背责、或降低工作难度,即使还可以用也会更换成新的,可能存在过度维护的隐性浪费。比如在TCL华星光电,由于大部分都是进口件,每年备件费用就数亿,通过东智设备健康管理EHM,构建精细化的备件生命周期管理,通过数据追踪备件的实际可运行周期,每年可节省数千万的成本。
从以上这些视角看,设备维护工作由过去的强调为生产服务,追求较高的设备完好率指标转变到以企业的经济效益为中心,要求设备管理工作重视维修费用的管理与控制,找到以最少的维修费用达到最高的设备可利用率的平衡点。企业的高层管理者如果能够从“投资”的角度认识维修和设备管理,将是十分宝贵的管理创新和理念转变。
图:设备管理的本质是找到维护平衡点
05 想依赖“预测性维护”解决问题,忽视了基础的数字化建设和数据积累。
“预测性维护”一直是工业互联网的热门话题,声称通过物联网和AI实现了预测性维护的公司繁多,工厂也期望将自己对设备故障的不确定性,交给 “预测性维护”来解决。但据笔者观察,目前大部分此类项目仍是概念和实验性的居多,在可解释性,可验证性、可复制性上都有问题。
预测性维护的落地比预想中困难,是因为企图单纯依赖数据提取可解释的工业机理逻辑,难度远超想象。这里主要两个原因:一是因为许多企业的基础数据还缺乏积累,比如设备基本的巡点检、维护保养、故障分析记录,都还是散落在各种纸张、Excel中,设备缺乏数字化档案,基本维护保养数据、备件更换记录、故障和修理数据,包括设备的故障特征数据还没有结构化的积累,就不可能实现模型的训练和验证。二是许多厂商企图单纯得依赖数据分析路径而忽略了设备工程师现有专业知识和经验的融入,光靠数学和AI算法容易走入统计陷阱,只是得到了相关性模型,不容易得出可解释的因果性的预测模型。
总的来看,设备之于工厂,就像枪之于战士。许多设备维护维修技术体系,也确实是从军队武器维护体系发展来的。构建新型的设备管理能力,需要工厂管理者,认识到设备之于工厂核心竞争力的基础性CONTROL ENGINEERING China版权所有,积极变革促使设备管理和作业方式,向数字化、智能化发展。根据Gartner预测,到2022年,60%以上的设备,将实现基于数据的智能运维方式,设备智能化管理和运维能力将会是衡量一个工厂核心竞争力的重要标志。最近国家工信部相关部门也正在起草和制定设备管理的国家标准、能力成熟度评估框架,将会对指导企业加强新型设备管理能力起到指引和促进作用。